The Problem
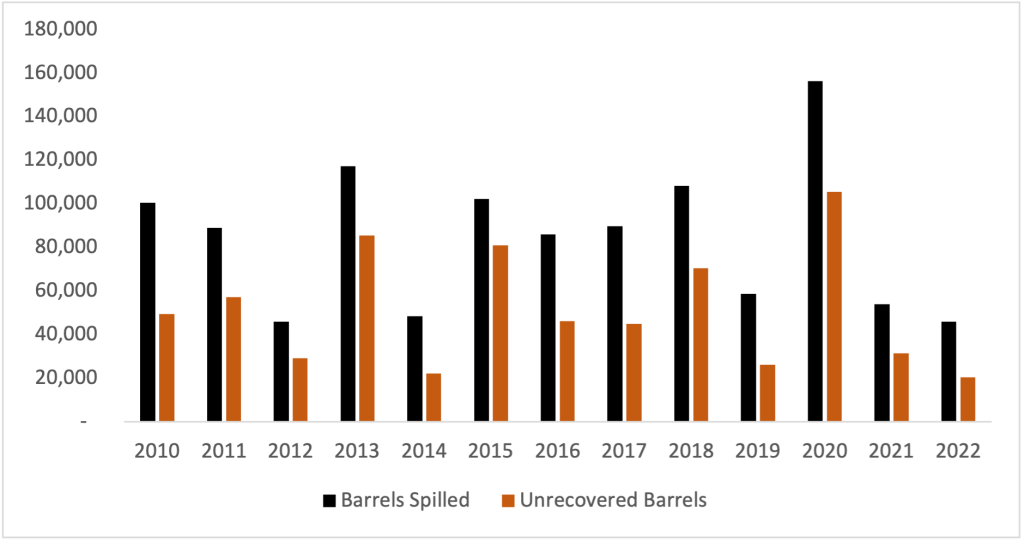
According to U.S. government data, pipeline spills of hazardous liquid happen almost daily. Estimate property damages caused by these spills have averaged nearly $300 million per year- and those expenses don’t account for regulatory fines, costs to reputation, and heightened insurance premiums and set asides.
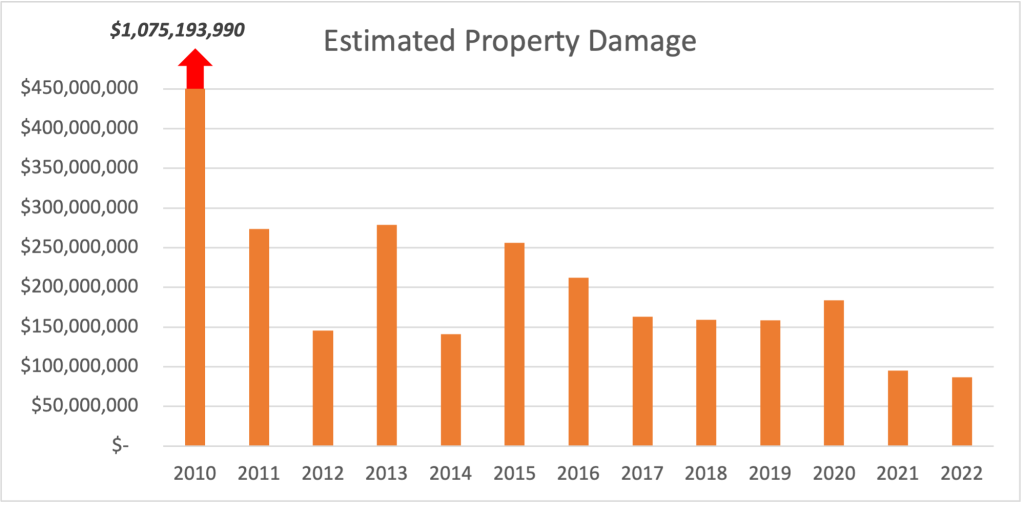
Moreover, the data demonstrates that while sophisticated data systems are important to identifying pipeline leaks, they often do not first identify them. In all the instances where SCADA or CPM systems are functioning properly, they are the initial indicators of only 9.6% of spills. Even in super spills (10,000 barrels leaked or more), these systems have initially identified just 1/3 of spills. 61% of hazardous liquid spills are still identified by on-the-ground personnel. In fact, these data systems could only detect 20% of leaks after they were identified. In particular, they failed to indicate any leakage of leaks below 500 barrels 83% of the time.
Even when sensors indicated a spill, human error can lead to spills continuing. The Marshall, Michigan oil spill sent alarms off in the control room. However, an EPA investigation found that the engineers thought the alarms were not indicating a spill but another issue. They overrode the alarms several times, leading to one of the largest oil spills in U.S. history.
The Solution
The patented Safe Crossings™ system uses the physics of internal pipeline pressure to safely prevent spills when a breach occurs in a Safe Zone. The system does not rely on sensors, remote controls, or human intervention to function. Instead, it uses nature to protect nature.
The system is comprised of four parts:
The Capacitor
Regulates pressure within the pipeline to enable the system to function optimally. The capacitor prevents pressure spikes when the Safe Zone is closed off during a pipeline breach and receives oil from upstream until the flow is stopped.
Pressure-actuated Valve
Reacting to pressure changes downstream, the valve shuts automatically if a breach occurs in the Safe Zone, stopping the flow of oil into the crossing.
Downstream Pump
During a breach, a pump on the downstream side of the Safe Zone creates negative pressure in the pipeline, drawing in any remaining oil in the crossing, as well as water or air from outside the breach, and preventing a spill into the environment.
Holding Tank
Beyond the pump, an optional holding tank can be used to store contaminated oil and water during a pipeline breach.
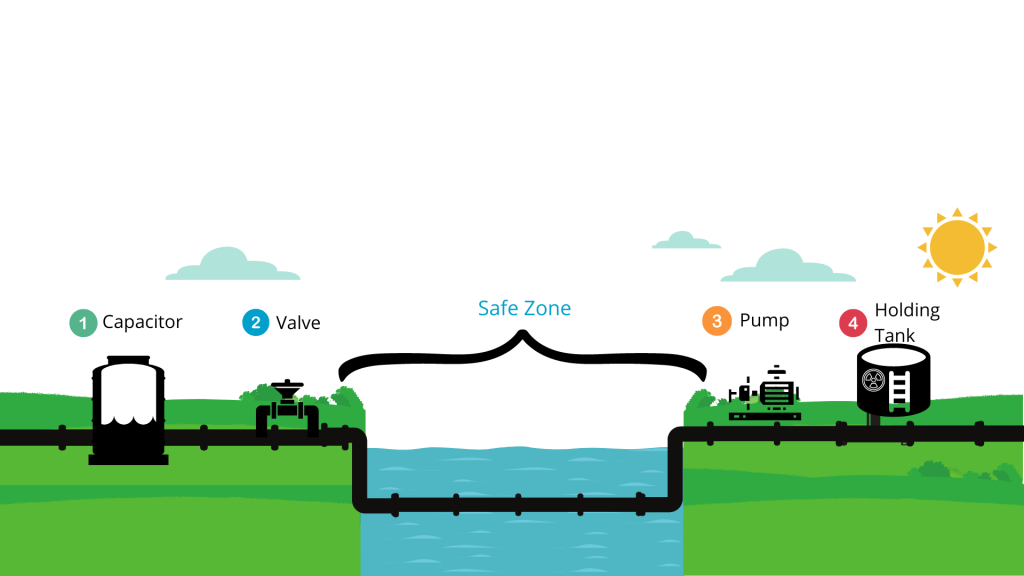
Together, each component of the system works to prevent leaks within the Safe Zone.
The Capacitor
The Safe Crossings system relies on pipeline pressure fluctuations within the pipeline to automatically close during a leak. The capacitor plays the important role of regulating pressure within the pipeline so the system works optimally. It also prevents pressure spikes upstream of the crossings when a breach occurs and the Safe Zone is quickly closed off. It will store oil pumped from upstream during an emergency closure until the pipeline controllers shut the system down.
The Pressure-actuated Valve
The second component of the system is the Safe Crossings pressure-actuated valve. As suggested in its name, the valve is sensitive to pressure changes in the pipeline. As illustrated below, optimal pipeline functioning results in pipeline pressure that holds the valve open during normal operating times. When a breach occurs in the Safe Zone, however, the pressure changes and results in immediate closure of oil into the Safe Zone.
The Downstream Pump
The pump on the downstream side of the Safe Zone is just like any other pump in the industry- it works to pump oil through the crossing and on downstream. However, when a breach in the Safe Zone occurs, the Safe Crossings system takes advantage of the fact that the downstream pump will continue to draw in oil from the crossing during a breach even though no more oil is permitted into the crossing. The pump then draws in remaining oil inside the pipeline and water and air from outside of the the pipeline and prevents oil from being released into the environment.
The Optional Holding Tank
Downstream of the pump, an optional holding tank can be installed that would store and contain contaminated oil during a pipeline breach. The system can divert oil contaminated with water, air, and environmental debris into a holding tank for processing, saving facilities downstream from cleaning if this cannot be easily accomplished. However, the system functions without the holding tank.